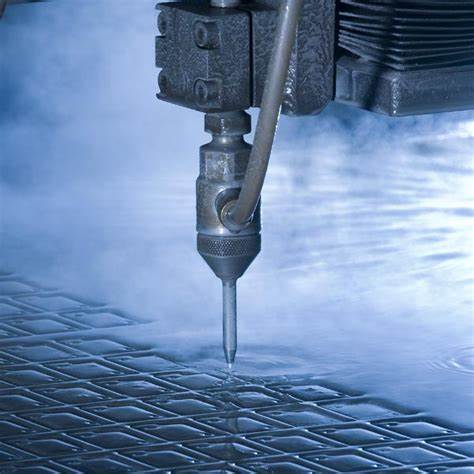
Cutting process and cutting speed of water jet cutting machines
Water jet cutting machines
(1) Water jet cutting method
There are two types of water jet cutting methods: low pressure water jet and high pressure water jet. Low-pressure water jet cutting is to use high-pressure water (14-69MPa) to pre-mix the cutting abrasive in a pressurized storage tank, and then send the mixed abrasive slurry directly into the cutting gun through a hose for cutting. The workpiece to be cut can be 500m away from the cutting power source. Or cut underwater. High-pressure water jet cutting is to convey high-pressure water (greater than 240MPa) and dry abrasives through their respective hoses, and then mix them in the mixing chamber of the cutting gun to complete the cutting process of objects, that is, shear and add For n kinds of materials, the workpiece Generally, it is carried out near the cutting power source.
When the low-pressure and high-pressure water jet cutting is cut under the same conditions, the water and cutting abrasive consumption of the former is 1/8 to 1/3 of the latter; from the perspective of the structure of the cutting torch, the low-pressure water jet cutting torch is relatively simple; In terms of energy consumption, low-pressure water jet cutting consumes less energy. Therefore, low-pressure water jet cutting is currently the most effective cutting method.
(2).Water jet cutting abrasive
The abrasives used for water jet cutting are mainly emery, olivine, garnet, copper slag and oxides. Among them, copper smelting slag is ideal. 1. The price is low, only 1/8 to 1/10 of fine steel grit; more importantly, its cutting speed is 30% faster than that of emery. This is because the particles of copper smelting slag are relatively sharp. During the cutting process, when they collide with the cutting workpiece, they are broken, thereby forming more cutting knives. In addition, when emery waterjet cutting is used, the cutting abrasive is easily embedded in the substrate, which will adversely affect some properties of cutting, such as the mechanical properties of welded joints. However, the use of copper smelting slag as a cutting abrasive can overcome this problem. defect.
Generally, the particle size of the cutting abrasive is required to be 0.2~1.5mm, which mainly depends on the nozzle diameter of the cutting spray gun. The cutting abrasive can be recycled and reused 2 to 3 times, and then filtered to remove the superfine abrasive.
(3). Materials used for water jet cutting nozzles
In addition to sufficient toughness and hardness, the cutting nozzle also has good wear resistance, which can effectively reduce the wear of the cutting nozzle and increase its service life. Due to the wear of the inner diameter of the nozzle, the notch gap will become wider, resulting in a decrease in the verticality of the notch section. Tungsten, silicon or cemented carbide are often used as materials for cutting nozzles, but the service life is not ideal. Sapphire is currently considered to be more suitable as a nozzle material.